総社カイタックが挑む工場DXとその先に目指すものとは
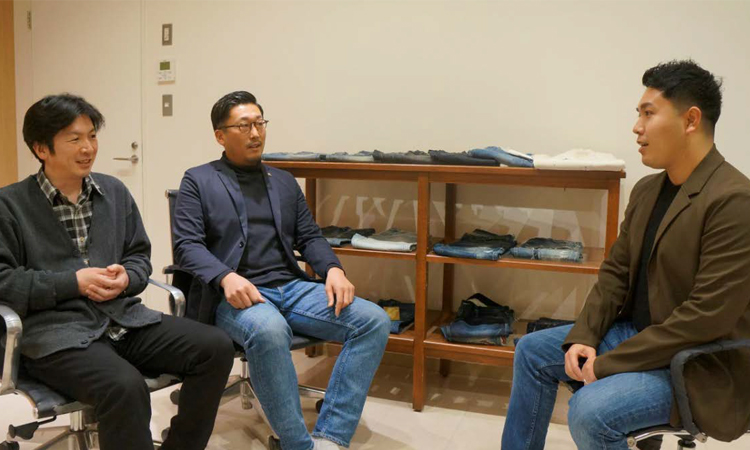
カイタックグループは時代と社会のニーズに応えた価値ある商品・サービスを提供しています。
同社は、ジーンズ生産工程のDX推進を強化し、東洋電装の生産管理システムの活用を工場の稼働率向上という成果に結びつけています。
両社に、DX推進に踏み出した背景や成果を上げるための活用法、今後の展望を聞きました。
- Project outline
-
- クライアント名:
- 株式会社総社カイタックファクトリー
- プロジェクト詳細:
- 生産管理システム導入
- 動画による動作分析
- 画像検査による検査工程の自動化
- Interviewee
-
- 株式会社総社カイタックファクトリー 工場長
- 横山巧
- 東洋電装株式会社
- 越智稔
- Interviewer
-
- 東洋電装株式会社
- 本多健太
好調がゆえの課題。生産計画の複雑化
-
総社カイタックファクトリー
横山巧 様
横山:当時総社ファクトリーでは自社のデニムブランド「YANUK」の生産を中心に行っていました。その中で、季節的流行的な理由から発注の変動が多くあるのに対して、工場側は毎月安定した生産を求める。その需給のアンバランスが原因となり、多くの在庫を抱える結果に繋がってしまいました。
本多:YANUKの安定生産への取り組みを大きく変える必要があったんですね。
横山:はい。だからと言って今からYANUK以外の仕事をとるのも困難な状況でした。国内のジーンズ生産は海外生産の製品に押され気味です。国内生産品はどうしても海外生産品に価格では勝てませんから。となると価格以外の面で勝負をすることになります。しかしそうすると多品種小ロットの非常に効率の悪い生産方法になり、価格は高いけど儲からない、受注にも山谷がある、という課題が発生します。
そこでカイタックグループとして「今一度コストに正面から向き合ってみよう!」という取り組みから「Made in Japanだけど低価格」という特長を持つ新しいブランド「オカヤマ デニム」を立ち上げました。YANUKの生産にバラつきがあり時期によって設備に空きがある総社ファクトリーで、このオカヤマ デニムの生産がスタートしました。
本多:YANUKとは逆のベクトルなので勇気のいる決断だったかと思います
横山:工場が仕事がなくて遊ぶくらいなら新ブランドの生産をしよう、という考えからの取り組みでした。おかげ様でうまくはまり、オカヤマ デニムは年々販売本数を増やすほど好調な結果を出せました。
しかしそのうち好調がゆえの問題が発生し始めました。高価格帯のYANUKのみの1オペレーションから、低価格帯のオカヤマ デニムの生産が加わり2オペレーションでの稼働になることで、全体の生産量が増え、工場の生産フローが煩雑化してきたのです。管理者の負担が増え、生産計画の精度が落ちることで生産効率が下がる結果となりました。この時、従来の管理方法のままでは限界があることに気付き、今までとは違う大幅な改善として工場のDXに踏み出す決断をしました。
本多:2オペになったことでのコスト面での問題はありましたか?
横山:低価格の製品の比率が多くなればなるほど採算が悪化することになるので、そういった面でも生産性の向上は必須でしたね。
本多:先ほど工場見学でも見させていただきましたが、洗い加工の工程が重要な部分だとか?
横山:2オペ稼働の工程管理の中で最も管理が複雑な工程が洗い加工でした。洗い加工はほかの工程とは違い、一つの設備をYANUKとオカヤマ デニムで共有する必要があります。なので設備稼働のスケジュール管理が非常に難しく、生産性の低下を招いている原因になっていました。
本多:洗い加工工程がボトルネックとなっていたのですね。
横山:はい。ただ、今回のプロジェクトを通していい気付きもあったんです。工場を見学した濱崎先生(広島工業大学)の目線で、洗い加工工程はすべての工程の中で最も付加価値を生む工程という側面も持っているということに気付きました。洗い加工はほかの工程に比べて、独自のノウハウや人の感性が必要な工程だといえます。「ネックになっている工程管理を改善し効率化を進めることで本来の付加価値を生む作業にもっと時間を使うことができる。それが工場全体の価値の向上につながる」とアドバイスをいただき、まずは洗い加工工程の管理方法の改善、デジタル化に集中してプロジェクトを進めていくことになりました。
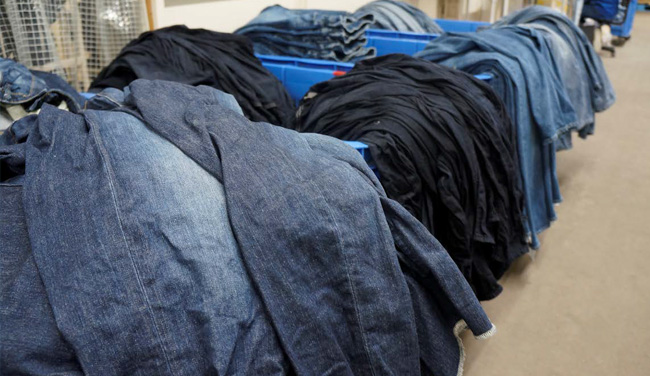
廊下に積まれた加工待ちの製品
2オペになることで生産フローが煩雑化し生産効率が低下した
低価格で導入でき、かつカスタマイズができる生産管理システム
-
エクセルを使った従来の生産管理表
横山:導入以前も加工工程は複雑だったので生産管理自体は必要でした。
メンバーの活躍で一部自動化をしたもののエクセルで管理を継続しており限界を感じていました。
本多:エクセルの画面を見させていただき驚きました。非常に複雑で丁寧な調整が必要そうですね。
横山:おっしゃる通りです。管理に非常に時間がかかる上に、精度を高めることが難しい状況でした。工程のスケジュール変更が頻繁にあるので、細かい計画を立てても変更にまた時間がかかってしまう。そういった事情もあり、変更に対応できるレベルの荒い生産計画を使用するしかなかったのです。計画の精度が低いことで、計画を順守する意識が弱くなり、悪循環が起きていました。そのような課題を解決するため、またさらに生産性を上げるために、生産計画の強化と見直しが必要でした。
初めは社内開発に挑戦したのですが、あまりにもオペレーションが複雑なため最適なシステムの開発が困難で、使いやすいシステムの完成にたどり着けないまま頓挫する形に終わりました。パッケージ化された市販のシステムを活用も検討しましたが、やはり当社の複雑なオペレーションには対応できません。
本多:そんな中弊社の生産管理システムを選んでいただけたのはなぜでしょう?
横山:私たちが東洋電装の生産管理システムを選んだのは、パッケージ化されたシステムをもとにオリジナルな要素を加えてカスタムできるという点が大きかったです。パッケージ品をベースにしているので完全オリジナルとは違いコスト面でも安心できました。
本多:越智さんにお尋ねします。
現場のユニークな工程に柔軟に対応できる仕様になった背景には、東洋電装も自身も製造業でDXに取り組んできたことが大きいでしょうか?
越智:そうですね。始めは弊社の工場での生産をデジタル化するための取り組みの一環でスタートした開発でした。
本多:既存の他社のシステムがたくさんある中で後発ながら開発にいたったのは、既存のパッケージ品では自社のユニークな部分にはまらなかったという経験が大きいんですかね?
越智:その通りです。中小規模の企業に生産管理のシステムが普及していない原因として第一にはコスト面ですが、次に自社のオペレーションに適応できないことが大きいと思います。低価格で導入できて、かつカスタマイズができる生産管理システムには高いニーズがあります。
本多:実際に使ってみて、良かった点はどこですか?
横山:スケジュールが変更になった際の計画変更時に、「直近1週間は変更しない」のように一部の期間を固定することができる点は魅力に感じています。また変更後のスケジュールを複数パターン用意してくれる点も助かっています。例えば、増加した作業分を計画に組み込む場合、①「普通の作業スピードのまま作業量が増えるので、本来の納期をオーバーする」パターンと、②「残業をしたり外注に頼んだりして納期を厳守する」パターンの2パターンから変更後の計画を選択することができます。
また、工場が稼働し標準タイムの記録を蓄積していくことで、どんどん計画の精度が上がっていく。使うたびにに成長していく部分も魅力です。進化していくためには現場の精度の高いデータ収集が必要です。その点は当社だけでは難しい部分でもあったので、東洋電装さんにデータ取りや分析も提案いただけたのはとても助かりました。
本多:越智さん、やはり自社のDXで35%の無駄を削減したという経験がこれらの提案に繋がった部分もあるのでしょうか?
越智:そうですね、市販の生産管理システムはIT分野の企業が作っていることが多いですが、私たちは同じ現場を肌で感じている分、より現場に寄り添った細やかな提案ができますし、その点は大きな強みだと感じでいます。
横山:その通りです!現場とシステム両方わかっている人が作ったシステムだから、当社の抱える課題にもマッチしたのだと思います。
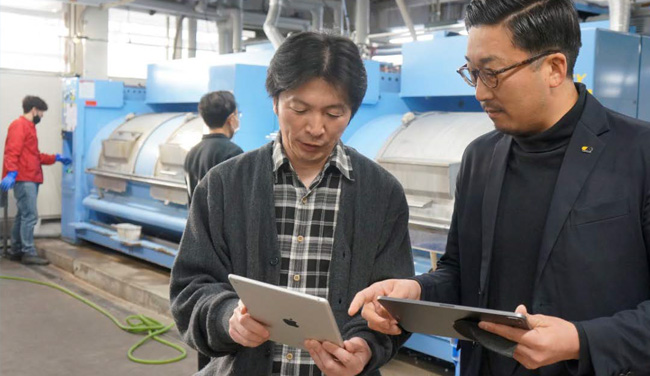
設備の稼働データを材料に成長し続ける生産管理システム
データドリブンで見えない課題の抽出、改善が可能に
-
東洋電装株式会社
越智稔
越智:そうですね、打ち合わせ時のジャストアイデアがきっかけでした。工場見学の際に見た多くの仕掛品が気になったんです。設備の横で順番待ちしている、工程のとまっている製品が多くありました。じゃあそこで工程が止まらないためには、設備がもう一台あればいいのか。いやそもそも今ある設備が100%無駄なく稼働できているのか?という疑問もあり、実際にデータをとって確認することから始めました。
本多:具体的にはどのような方法でデータを収集したのですか?
横山:先ほど話した洗い加工の設備である窯2台に対してカメラを3台設置して画像を分析しました。具体的には①窯が稼働しているのか、②窯の前に人がいるのか、その時間や回数をデータとして収集しました。
本多:窯と人、両方の動きを分析対象としたのはなぜですか?
横山:たとえば、「窯が稼働している+窯の前に人がいる」場合、これは少し効率が悪い状態です。窯が稼働している間、窯の前で人が行う仕事はありませんから。「窯が停止している+窯の前に人がいない」場合、これが一番効率が悪い状態です。窯が空いているなら今すぐ稼働させて稼働率を上げなければいけません。このように窯の動きと人の動き両方の組み合わせで、より細かな稼働状況が把握できます。
本多:分析してみて、どのようなことがわかりましたか?
横山:データを分析して分かったことは、2台の窯で稼働率が大幅に違ったことです。サイズの大きい窯Aの稼働率は80%だったのに対し、サイズの小さい窯Bの稼働率は30%でした。仕掛品が大量にある状況なのに窯Bは殆ど稼働していなかったということです。てっきりフル稼働していると思っていたのでこの結果には私自身も驚きました。それまではフル稼働した上での大量の仕掛品なのであれば改善の余地はないとあきらめていましたから。
東洋電装株式会社
本多健太
本多:なぜ2つの窯の稼働率にそれほどまでの差が出るんですか?窯Bを使わない理由があるんでしょうか?
横山:はい、このデータをもとに現場のスタッフにヒアリングを行いました。2つの窯は同じタイプのサイズ違いなのですが、サイズの大きい窯Aの方が効率よく加工ができます。なので効率のいい窯Aを優先的に使っているようでした。
また、窯Aと窯Bとでは若干加工の仕上がりに色味の差が出るので、窯Bの使用を避けがちだということもわかりました。
本多:稼働率の差は改善されていますか?
横山:現在、完全に改善されたされたわけではありませんが、現場のスタッフも数字で状況を示されると意識せざるを得ないのだと思います。品質に問題がない範囲で工夫をし、今まで稼働率が低かった窯の方も以前より稼働するようになりました。
越智:先ほど工場を見させていただきましたが、初めて小さい方の窯(窯B)が動いているのを見ましたよ。このデータをもとに横山さんが現場スタッフにお話された影響が出ていますね。
今回の取り組みは完全にデータドリブン。そこが大きいですね。
本多:データドリブンで課題が明確化し、それが現場を動かす大きな説得材料になったのですね。
横山:現場スタッフは精一杯やってくれています。そのうえで本人たちも気付けていない課題が発生している。もちろん私たち管理者側も一つの工程に貼りついてみているわけじゃないので気付けません。今回カメラを付けて得たデータを数値して目の前に突き付けられたことで初めて課題に気付くことができました。データで稼働状況を見える化していなかったら、管理者側は動いていない窯に気付かず、現場スタッフも窯を動かさないまま仕掛品が増え、残業や休日出勤で工場全体が疲弊するという悪い状況がずっと続いていたかもしれません。
本多:見える化を通して改善の余白があったことに気付けたのは大きな成果ですね。
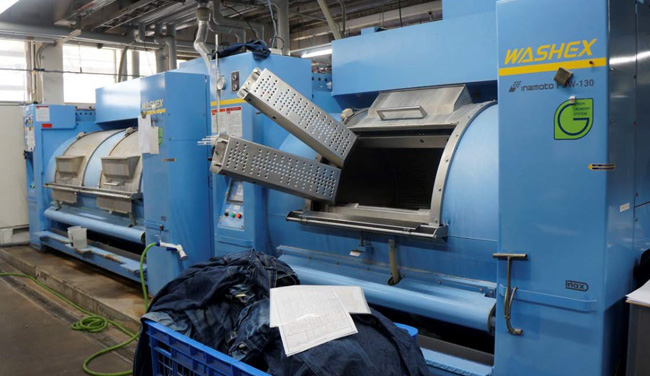
カメラで稼働状況を分析したことで稼働が十分ではない設備があることが分かった

3台のカメラ映像はアプリで一括管理。設備と人の状態をデータとして収集した。
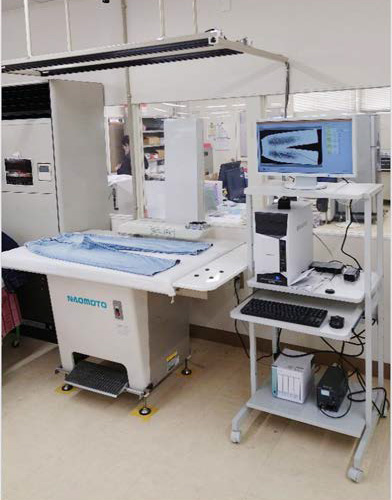
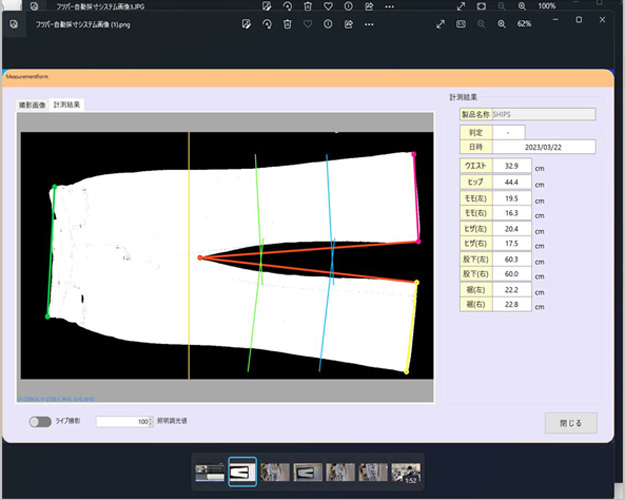
自動採寸システム
全て手作業で行っていた仕事の自動化に成功した
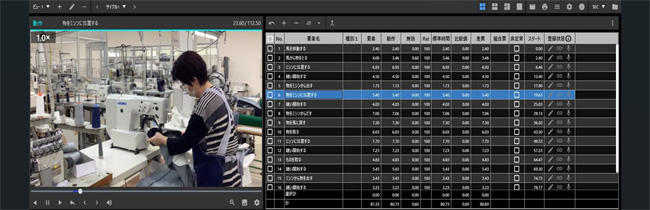
動作分析システム
職人を輝かせることが製造業の未来を創る
-
本多:今回のプロジェクトを終えていかがですか?
越智:今ある成果だけじゃなくて、データを蓄積することで今後も持続的に改善がしていけるということは、今回やってかなり良かった点だと思います。それは東洋電装での取り組みを通しても感じています。
現場のスタッフも、まさか自分たちの作業のデータを取られると思ってないはずです。今回の取り組みをきっかけに、そういった現場でのDXの意識が高まってくることも期待できますね。次こっちくるぞ!って。
横山:一つの箇所で結果が出たら、次への意識が生まれます。一つの工程で結果が出たなら、今度は頭からおしりまでシステムでつなげたいな、と。生産管理システムも、今は洗い加工と仕上げ加工のあいだのみですが、今後全体を網羅できるシステムに進化していけると確信しています。今回の取り組みが工場のDXがどんどん広がっていくきっかけになりました。それは大きな成果ですね。
越智:一気に全工程にシステムを入れたりデータ取りしたりするのはハードルが高いです。まずは一つの工程、一つの現場からスモールスタートすることがDX推進の最適な一歩になると思います。
横山:100万円のシステムを入れて失敗したとしても、「前向きな失敗だよね」でそこで終了してしまうパターンは結構あると思います。デジタル化の一歩目は意外とみんな踏み出してる。でも一歩目から二歩目に進めるかが大事ですよね。一歩目から二歩目、二歩目から三歩目と続けて足を前に出せるようになれば、どんどん進んでいけるんです。
越智:一歩目も二歩目も、私たちが同じ製造業で、似た環境や悩み、課題を共有しているからこそ踏み出せたと思います。何をやったらいいか分からない、という時にこのチームがあったから、互いに意見を出し合ってやるべきことを見つけることができました。
本多:今後、現場がどういう状態になっているのが理想だと思いますか?
横山:今の当社は、同じ敷地にありながら各部署同士がうまく繋がっておらず、情報共有ができていない状況です。せっかく一貫生産が武器だと言っているのに、非常にもったいないことです。この工場がDXを通じて真の意味でつながれば一貫生産工場である本当の強みが発揮され価値向上できると思います。それを楽しみにしています。
本多:それが実現された際には何が起こっているでしょうか?越智さんまとめてください!笑
越智:職人が活躍する現場でも付加価値を生んでいない作業が多く残っています。
そこをデータドリブンで変革することがものづくりにおけるデジタルトランスフォーメーションであり、それによって職人の価値を向上させることができます。それが低迷している日本の一次産業復活のカギになり、引いては世界で日本が勝負するための原動力になると信じています!
こんな感じでいかがでしょうか?
本多:ありがとうございます!かっこよくまとまったところで終了のお時間となりました。
横山さん、越智さん、今日は本当にありがとうございました。
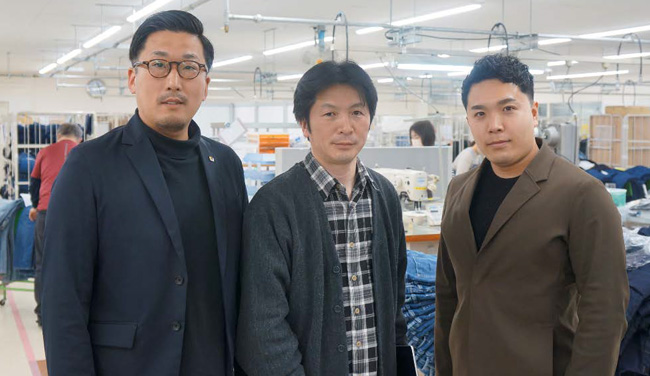
株式会社総社カイタックファクトリー
アパレルメーカー・カイタックグループのジーンズ製造子会社として、2019年3月に分社し設立。
国内の同規模企業としては唯一の1つの工場内で裁断から縫製・洗い加工・検品仕上げまでのジーンズ製造の一貫生産体制を持っています。現在は、高付加価値商品「YANUK(ヤヌーク)」や量販店・低価格専門店向け商品「オカヤマ・デニム」など受注のおよそ9割がグループ内ブランドの生産請負となっています。
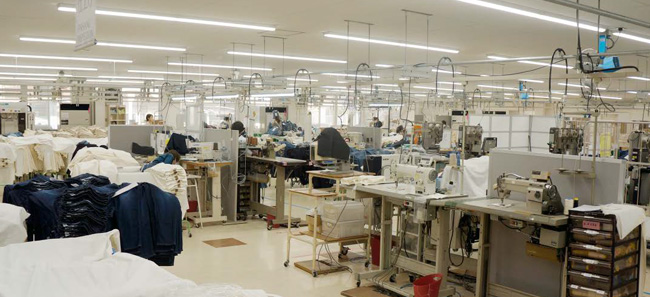