- はじめに:副社長(現社長)の決断から始まったDXの道のり
- 1. コミュニケーションのDX
- 導入背景と課題
- 導入のあゆみ
- 効果と成果
- 2. ペーパーレス化のDX
- 導入背景と課題
- 導入のあゆみ
- 1. 経理部門のペーパーレス化とデジタル化
- 2. 設計・製造部門でのデジタルトランスフォーメーション
- 3. 社内全体でのデジタルトランスフォーメーションの取り組み
- 効果と成果
- 3. 業務効率化のDX
- 導入背景と課題
- 全体的な取り組み
- 製造現場の効率化
- 購買チームの取り組み
- 成果と展望
- 地域未来牽引企業選出とDX工場見学の実施
- おわりに:DX推進は続いていく挑戦
ペーパーレス化から製造現場の効率化まで!
DXで変わる働き方
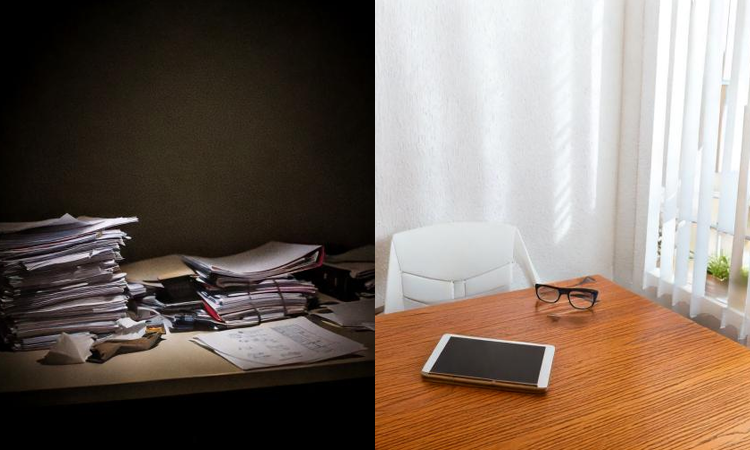
はじめに:副社長(現社長)の決断から始まったDXの道のり
2012年、当時の副社長(現社長)の決断により、社内ITプロジェクトが本格的に動き始めました。
紙と手作業を中心としていた従来の業務体制を見直し、IT技術を活用した業務改革を進めることで、将来的な競争力を高めることを目指したのです。
この取り組みは、単なるシステム導入に留まらず、業務フローの見直しや従業員の意識改革を含む、全社を挙げた大規模なプロジェクトとなりました。
その第一歩となったのが、2012年12月に導入されたサイボウズofficeでした。このツールをきっかけに、社内のコミュニケーション改善やペーパーレス化、そして業務効率化のためのDXが本格化していきました。
- あわせてご覧ください
- ▷ コレを見ればすべてわかる!? 東洋電装グループ50年の歴史
1. コミュニケーションのDX
導入背景と課題
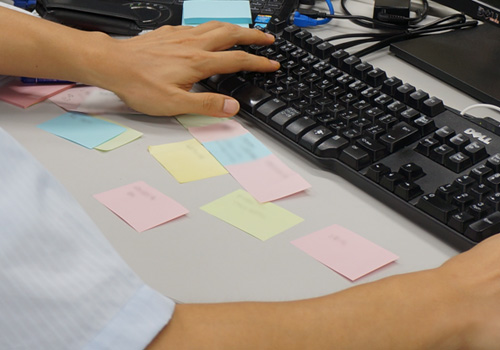
手書きのメモが
机上にたくさんあった頃
2012年頃、東洋電装グループの従業員数は約20人でしたが、ちょうど事業拡大期を迎えていました。
拠点や社員数の増加に伴い、物理的な距離がコミュニケーションの課題となり、それを解決する手段としてDX(デジタルトランスフォーメーション)が必要とされるようになったのです。
従来の手書きメモや対面依存の連絡では情報の行き違いが多発することは目に見えており、デジタル化による効率化が必要となりました。
導入のあゆみ
- 2012年12月
- 「サイボウズOffice」を導入することで、社員のスケジュールをデジタル化し共有を推進(現在はサイボウズGaroonと併用)。
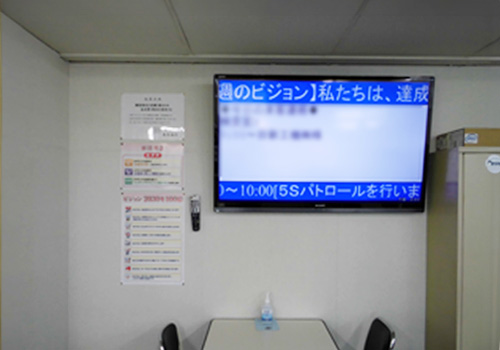
稼働当時
周知事項が掲載されていた
- 2013年7月
- 社内デジタルサイネージを活用し、社内全体への周知を効率化(現在は廃止)。
- 2016年以降
- Skype、Slack、Chatworkなど、時代や利用ニーズに応じてツールをアップデート
- 2023年6月
- 「Teams」を導入し、社内外のコミュニケーションツールを統一
効果と成果
グループウェアの活用で「言った言わない」のトラブルが減少したほか、メモや情報のデジタル化によりフリーデスクや現場作業者も迅速に情報共有が可能になりました。
また、コロナ禍以前からZoomの導入や限定的なリモートワーク対応が進んでいたことで、コロナ禍においてもリモートワークやテレビ会議に柔軟に対応でき、現在ではフルリモート社員も数名いるほどコミュニケーションのDXは働き方の柔軟さにも繋がりました。
“当たり前”な風景が変わっていった
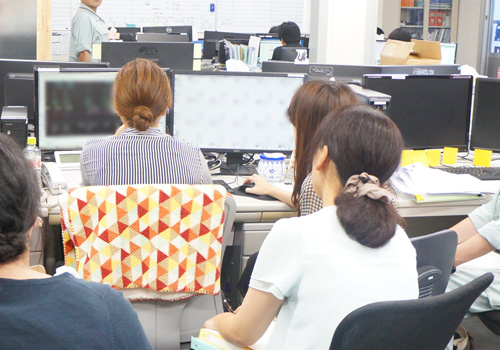
1つの画面に人が集まって情報共有MTG
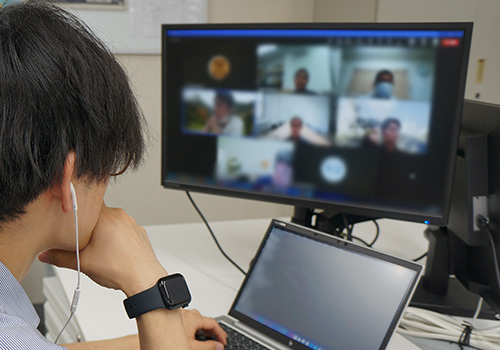
それぞれの場所でテレビ会議に参加
2. ペーパーレス化のDX
導入背景と課題
図面を多く扱う業務特性や、承認プロセスでの紙依存により以下の課題が顕在化していました
- 保管スペースの限界と、物理的資料の検索効率の低さ
- 紙コストと環境負荷の増大
- 従来の紙ベースの承認ルートが業務進行を遅らせる原因に
- 作業現場での図面更新が煩雑で、リアルタイム性に欠けていた
導入のあゆみ
1. 経理部門のペーパーレス化
- 2020年4月
- 「ネットde顧問」を導入し、給与明細のデジタル配布を開始
物理的な紙の給与明細が不要に
- 2022年6月
- 「Jinjer」「freee会計」を導入し、Excel様式の印刷・手書き追記・承認のプロセスを完全デジタル化
申請から承認までがスムーズに
2. 設計・製造部門のペーパーレス化
- 創業当時
- ドラフターを使った手描き図面が主流
- 1992年頃
- CADシステムの「GMM-1000」を導入し、一部設計作業をデジタル化
- 2003年頃
- 「AutoCAD」の導入で設計効率が向上
- 2016年頃
- 「BricsCAD」「ACAD-DENKI」を導入し、設計作業の精度とスピードがさらに向上
時代に応じて設計作業ツールも変わっていった
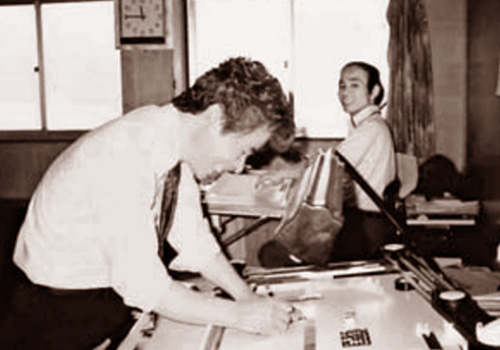
手書きで設計を行っていた頃
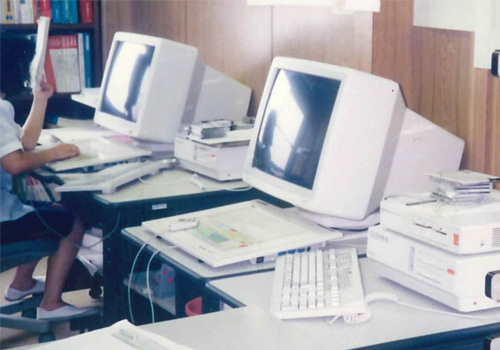
GMM-1000での作業風景
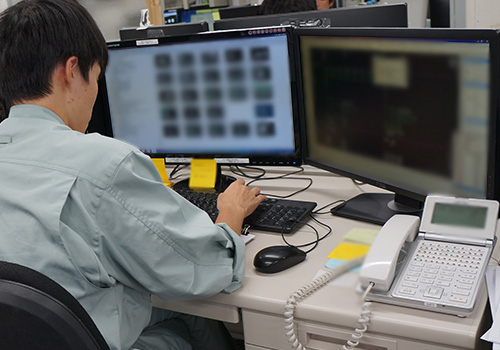
AutoCADでの設計作業
- 2022年
- 可部事業所の開所に伴い、製造部でタブレットを導入
作業用図面のデジタル化が進み、現場作業者が最新の図面をリアルタイムで確認可能に
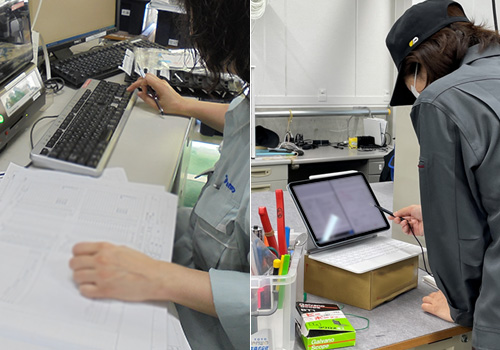
左:紙とパソコンを使用した作業が 右:タブレット1台で完結するようになった
3. 社内全体での取り組み
2013年よりグループウェア上で複合機のチャージ料を月次で周知し、社員に印刷コストの可視化を行い、不必要な印刷を減らす意識付けを実施することで、デジタル化の推進を図りました。
これらの取り組みは、社内でのDXと効率化を推進するうえでおすすめです。
- 補助策
- デュアルディスプレイの導入を推奨することで、デジタル化を進め、紙資料を参照せずに効率よく作業が行える環境を整備しました。
効果と成果
4つの点で効果が現れました。具体的には以下の通りです。
- コスト削減
- 印刷費用や紙保管スペースが大幅に削減
- 作業効率向上
- 現場作業者がタブレットで最新の図面を即時確認できるようになり、作業ミスや無駄を削減
- 環境負荷軽減
- 紙使用量の削減が進み、環境配慮の意識向上に寄与
- 承認プロセスの迅速化
- デジタル化されたシステムにより、承認業務のスピードが向上し、全体的な業務効率化につながった
3. 業務効率化のDX
導入背景と課題
業務効率化は、コミュニケーションやペーパーレス化と密接に関連していますが、特に以下の課題解決を目的として取り組んできました。
- 社内外での情報共有不足による無駄な時間の発生
- 製造現場での効率的な作業手順の確立
- 管理業務における非効率な承認・記録プロセスの改善
全社的な取り組み
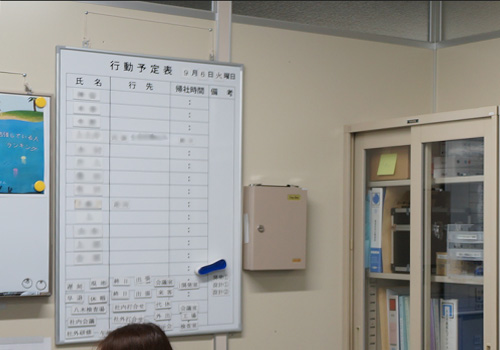
社員の予定把握と言えば
ホワイトボードだった
- 2012年12月
- 「サイボウズoffice」の導入により、社員の予定や行先を即座に把握できる環境を整備
これにより、社員を探す手間が削減され、時間の無駄が解消されました
また、物品購入などのワークフローをグループウェアで一元化することで、紙スタンプラリーが軽減しました
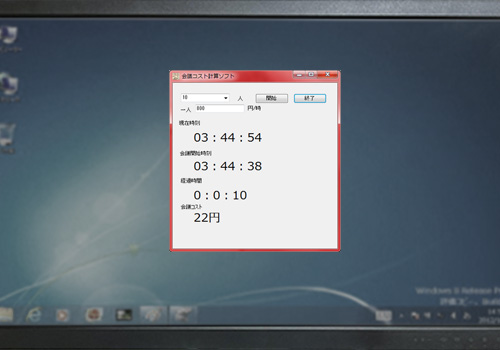
時間×人数×時給で1秒単位でコストを算出する仕様
- 2013年
- 自社開発の「会議コスト計算ソフト」を導入(現在は廃止)
人数と一人当たりの時給を入力することで、会議時間に応じたコストを表示する仕組み
会議のコストを「見える化」し、不要な会議を削減する意識を高めるとともに、会議時間の短縮を促すきっかけとなりました
- 2014年
- 「SMILE BS」を導入し、案件ごとの販売管理をExcelからシステム化
これにより、過去の販売データも容易に検索可能になり、データ活用が進展しました
- 2016年
- Skype導入によるWeb会議の普及で、移動時間の削減を実現
その後、ZoomやTeamsとツールは変わったものの、社員の習慣化も進み、さらに効率的な会議運営が可能に
- 2020年
- 「ネットde顧問」により勤怠関連の手続きがデジタル化
社員情報がシステム上で管理され、社労士事務所との情報共有もスムーズに
- 2022年
- 「Jinjer」「freee会計」の導入で、経費精算や承認業務がPCやスマートフォンからでも実施可能に
申請から承認までのプロセスが迅速化
また、同時期よりRPA(ロボティック・プロセス・オートメーション)を導入し、単純作業の効率化を実現
これにより、手作業に頼っていたデータ入力や報告書作成などの作業時間を短縮し、人為的ミスの削減にもつながった
- 2024年
- Microsoftのローコードプラットフォーム「Microsoft Power Platform」を導入し、非技術者でもビジネスアプリを開発できる「Power Apps」を活用
社内で「こんなツールがあったらいいな」と思う業務改善アイデアを次々とアプリ化
製造現場の効率化
広島工業大学との実証実験をはじめ、製造現場でもデジタル技術を活用した効率化を推進しています。
ネットワークカメラシステムを活用した動画分析により特定されたボトルネックをもとに改善を行った結果、35.6%作業時間が短縮し作業効率の向上を実現した事例を5点ご紹介します。
- 配線ルート設計の共有化
- 従来:職人が集まって打ち合わせを繰り返し設計
- 改善:タブレット上で加筆・修正した配線ルートを即時共有可能に
- 効果:後戻り作業が減少し、非熟練作業者でも作業可能に
- 部材の仕様共有
- 従来:職人が図面をもとに部材の長さを微調整
- 改善:設計者が「取付図」を作成し、部材の穴位置や長さを明確化
- 効果:組み立て作業の約30%の労務削減に成功
- 標準品と特殊品の違いの明確化
- 従来:標準品と特殊品の相違を都度確認しながら作業し4倍の時間がかかっている
- 改善:相違箇所を図面に記載し、作業者が重要点のみ確認
- 効果:特殊品の組み立て時間が大幅に短縮
- 工場レイアウトの最適化
- 従来:空きスペースに棚や作業台を配置し作業効率は重視されていない状態
- 改善:動線や物流の流れを考慮し、棚や作業台を再配置
- 効果:移動に伴う時間ロスが減少し作業効率が大幅に向上
- 専用工具の導入
- 従来:共有工具を使用した後に定位置へ戻す必要があり作業に時間的ロスが発生
- 改善:各作業者に専用工具を付与し共有工具の使用を最小化
- 効果:共有工具の取り回しが不要になり作業時間が大幅に短縮
購買チームの取り組み
従来は各部署がバラバラにFAXで注文を行い、案件ごとの物品を管理するのに苦労するだけでなく、取り違えによるトラブルも発生していました。
この課題に対し、購買チームを立ち上げ、物品管理の集約化を実施。
さらに、FAXからメールを活用した注文フローに切り替えることで、効率化とペーパーレス化を一体的に進めました。
成果と展望
これらの取り組みにより、社内外での効率的な情報共有、製造現場での生産性向上、承認業務の迅速化を実現しました。
DXの次のステップとして、AIやIoT技術を活用したさらなる業務最適化を目指しています。
地域未来牽引企業選出とDX工場見学の実施
東洋電装は、2018年には「地域未来牽引企業」に選出され、さらに2024年には「はばたく中小企業・小規模事業者300社」のDX部門で受賞するなど、当社の取り組みは外部からも高く評価されています。
このような実績を背景に、2022年より同じ中小製造業向けに「DX工場見学」を実施。
自社の成功事例や取り組みを公開し、地域の製造業全体のデジタル化を支援しています。
おわりに:DX推進は続いていく挑戦
2012年に始まった社内ITプロジェクトは、決して一夜にして完成したわけではありませんでした。
小さな一歩からの試行錯誤の連続であり、その積み重ねが現在のDXの基盤となっています。
DXは全てを一度に変える必要はなく、自社に合った形で少しずつ進めていくことが重要です。
私たちはこれからも社内でDXを進めるとともに、FRICS Fabという事業を通じて、同じ課題に直面する中小製造業の皆様をサポートしていきます。
ぜひ、私たちが試行錯誤の中で培ったシステムや取り組みを体験いただけるDX工場見学にお越しください。
ともに未来を切り拓いていきましょう。
- DX工場見学の詳細はこちら
- ▷ 35.6%の無駄を削減した東洋電装のDX工場